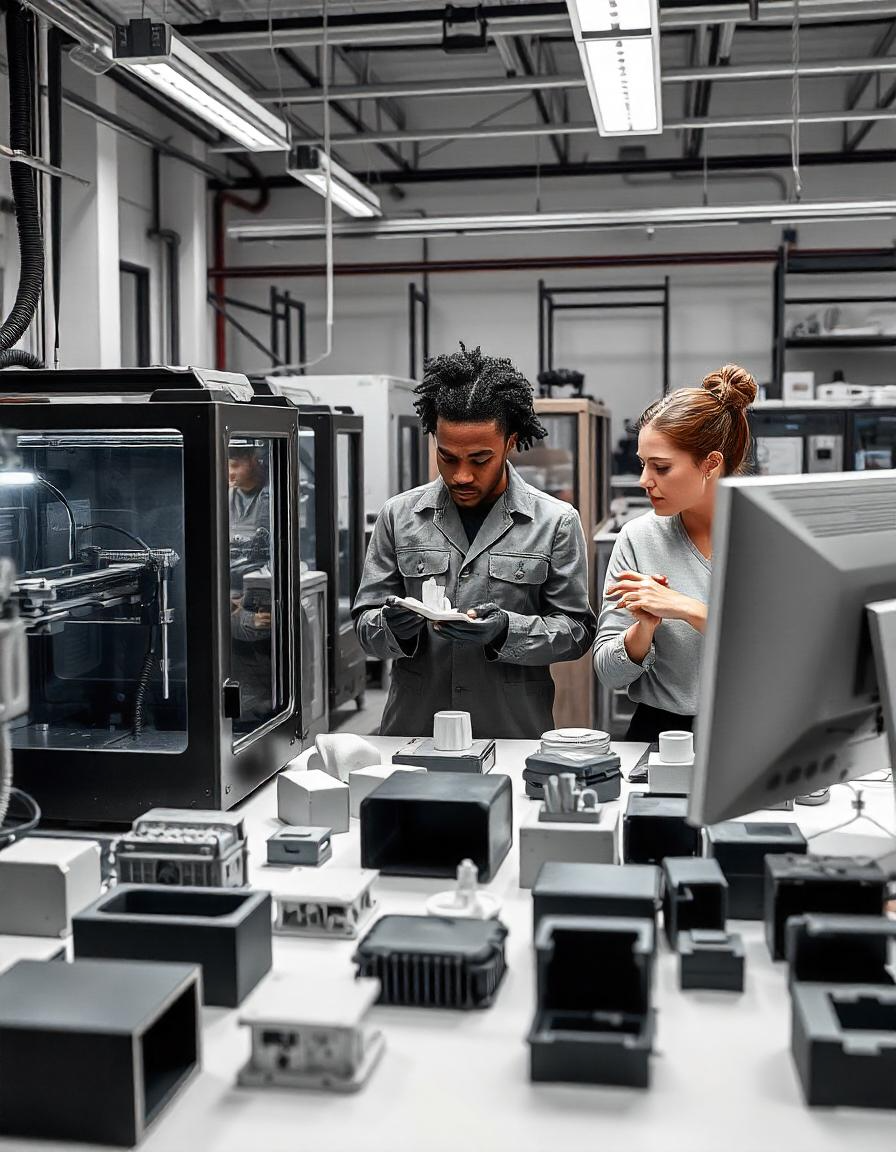
How to Choose the Perfect Plastic Enclosure for Your Electronic Project
When designing an electronic project, choosing the right enclosure is critical. It protects your components, enhances aesthetics, and influences functionality. Traditionally, injection-molded enclosures have been the go-to option, but recent advancements in 3D printing technology offer a compelling alternative. In this blog, we’ll explore how to choose the perfect plastic enclosure and why 3D-printed enclosures might be the superior choice for your needs.
1. Understand Your Project Requirements
Before selecting an enclosure, it’s essential to define your project’s specific needs:
-
Size: Ensure the enclosure accommodates all components comfortably, with room for airflow if needed.
-
Mounting Options: Consider whether you need wall mounts, desk stands, or other attachment methods.
-
Material Properties: Evaluate the need for durability, heat resistance, or chemical resistance.
-
Aesthetics: Decide if the enclosure’s appearance matters for showcasing or branding.
2. Traditional Injection-Molded Enclosures: Limitations
Injection molding has long been the standard for plastic enclosures, offering:
-
Mass production at a consistent quality.
-
A wide range of material choices.
However, injection molding has significant downsides:
-
High Initial Costs: The tooling required for injection molding is expensive, making it impractical for low-volume production or prototypes.
-
Limited Customization: Customizing a mold is costly and time-consuming.
-
Minimum Order Quantities: Most manufacturers require large production runs, which is unsuitable for small-scale projects or experiments.
3. The Advantages of 3D-Printed Plastic Enclosures
3D printing is revolutionizing how enclosures are designed and produced. Here’s why you should consider it:
a. Cost-Effective for Prototypes and Small Runs
With 3D printing, there’s no need for expensive molds or setup fees. This makes it ideal for:
-
Prototypes.
-
Small production batches.
-
Custom, one-off designs.
b. Unmatched Customization
Unlike injection molding, 3D printing allows complete freedom in design. You can:
-
Create unique shapes tailored to your project.
-
Incorporate branding, such as logos or text, directly into the design.
-
Easily modify designs as your project evolves.
c. Fast Turnaround Time
3D printing eliminates the lengthy tooling process. You can:
-
Go from concept to finished product in days.
-
Quickly iterate designs without costly delays.
d. Wide Range of Materials
Modern 3D printing offers a variety of materials to suit your needs:
-
Durable ABS or PETG for robust applications.
-
Flexible TPU for impact resistance.
-
Specialty materials with heat or chemical resistance.
e. Sustainability
3D printing minimizes material waste compared to injection molding, making it an eco-friendlier option. You only use the material required for the enclosure, reducing excess plastic.
4. Factors to Consider When Choosing a 3D-Printed Enclosure
If you decide to opt for a 3D-printed enclosure, consider the following:
-
Design Complexity: Leverage 3D printing’s ability to create intricate designs that traditional methods can’t.
-
Finish Quality: Choose a provider that offers post-processing options like sanding or painting for a professional look.
-
Material Selection: Ensure the material aligns with your project’s requirements.
-
Lead Time: Confirm that the provider can deliver within your timeline.
5. When to Choose 3D Printing Over Injection Molding
-
Prototyping: When you need to test and refine your design.
-
Low-Volume Production: For limited runs of enclosures.
-
Customization: When your project requires unique or intricate designs.
-
Time-Sensitive Projects: When you need enclosures quickly without sacrificing quality.
Conclusion
Choosing the right plastic enclosure is vital for the success of your electronic project. While injection-molded enclosures remain suitable for mass production, 3D-printed enclosures offer unparalleled advantages for prototyping, customization, and small-scale production. Their cost-effectiveness, speed, and design flexibility make them a smart and efficient choice for makers, hobbyists, and professionals alike.
Ready to elevate your project with a custom 3D-printed enclosure? Explore our range of high-quality, tailor-made enclosures designed to meet your specific needs. Contact us today to get started!